Increasing awareness of environmental sustainability has provoked rubber scientist and rubber compounder to develop green polymer and bio-based rubber chemicals when designing rubber compound formula. The concept of green polymer is implemented with the development of specialty natural rubber. Specialty natural rubber is made by chemical modification of natural rubber mainly in latex phase to substitute petro-based synthetic rubber.
Natural rubber has weakness which can limit its usage in the manufacture of rubber goods primarily for outdoor application. Naturally, natural rubber exhibits low thermal oxidative aging resistance and swelled when immersed in oil or hydrocarbon solvent. This is due to the presence of high degree of unsaturated C double bond in its molecular chains and non-polar character of natural rubber although it also show high molecular weight with wide polydispercity index.
Commercial natural rubber latex is a white milky sap biopolymer derived from exploitation of rubber plant Hevea brasiliensis Muell Arg. Natural rubber molecules form 1,4 cis-configuration which composed of repeating monomer units of isoprene (2-methyl-1,3-butadiene). This biopolymer is highly potential to be modified chemically to enhance the property. Referred to Hashim and Ong (2007), chemical modification of natural rubber latex can be conducted through the following procedure :
- Modification by bond rearrangement without introducing new atoms which lead to changes in the chemical structure and/or reduction in molecular weight. Ex : cyclization, deproteinization
- Modification by introducing a chemical group via addition or substitution reactions at the unsaturated double bonds. Ex : epoxidation, hydrogenation
- Modification by grafting with one or two molecules usually vinyl monomers at the allylic carbon. This method is often applied in the synthesize of thermoplastic natural rubber. Ex : graft copolymerization of MMA ad styrene into natural rubber latex
Research Center for Rubber Technology – Indonesian Rubber Research Institute (IRRI) has successfully developed a type of specialty natural rubber such as epoxidized natural rubber (ENR), hydrogenated natural rubber (HNR), and graft copolymerization MMA/Styrene/NR (NR-g-MMA/St) at laboratory scale. HNR was produced by IRRI had 60% degree of hydrogenation. This type of specialty natural rubber is regarded as promising material to substitute EPDM and Chloroprene rubber. Meanwhile, ENR is potential to be used to replace NBR as base material for oil resistant rubber product. Furthermore, the possibility usage of NR-g-MMA/St still need to be explored, one of them is an additive for polymer modified asphalt to eliminate Styrene Butadiene Styrene (SBS) role.
In line with the development of specialty natural rubber, researchers are also has great interest in developing bio-based rubber chemicals. Rubber chemicals are added during rubber compounding process to improve rubber performance. Rubber chemicals include processing aid, rubber processing oil, reinforcing filler, antioxidant, antiozonant, activator, accelerator, and vulcanizing agent. Bio based rubber chemicals are made from renewable natural source.
Sulfur vulcanization of vegetable oil at high temperature can produce brown factice. Brown factice is a cheap extender rubber-like material. The visualization of brown factice could be categorized from its colour, from yellow, brown to dark brown. Using brown factice in rubber compound improves the process-ability of the compound during extrusion and injection moulding, furthermore it is also provide excellent dimension stability of the rubber product. Therefore, brown factice mainly use during the rubber seal and rubber hose manufacturing.
Pine tar oil is sticky dark liquid resulted from destructive distillation of wood of various trees of the family Pinaceae. This material is regarded as alternative bio plasticizer or rubber processing oil to substitute petro based aromatic oil. Pine tar oil play important role in increasing adhesion strength (rubber to rubber) of rubber compound. Therefore, pine tar oil is suitable to be added in rubber compound formulation for production of cushion gum. Cushion gum is a thin intermediate rubber compound layer which is applied on the casing outer surface to bond the pre-cured tread as adhesion medium of retread tyre.
Santi Puspitasari
Rubber Technology Researcher
Research Center for Rubber Technology
Indonesian Rubber Research Institute
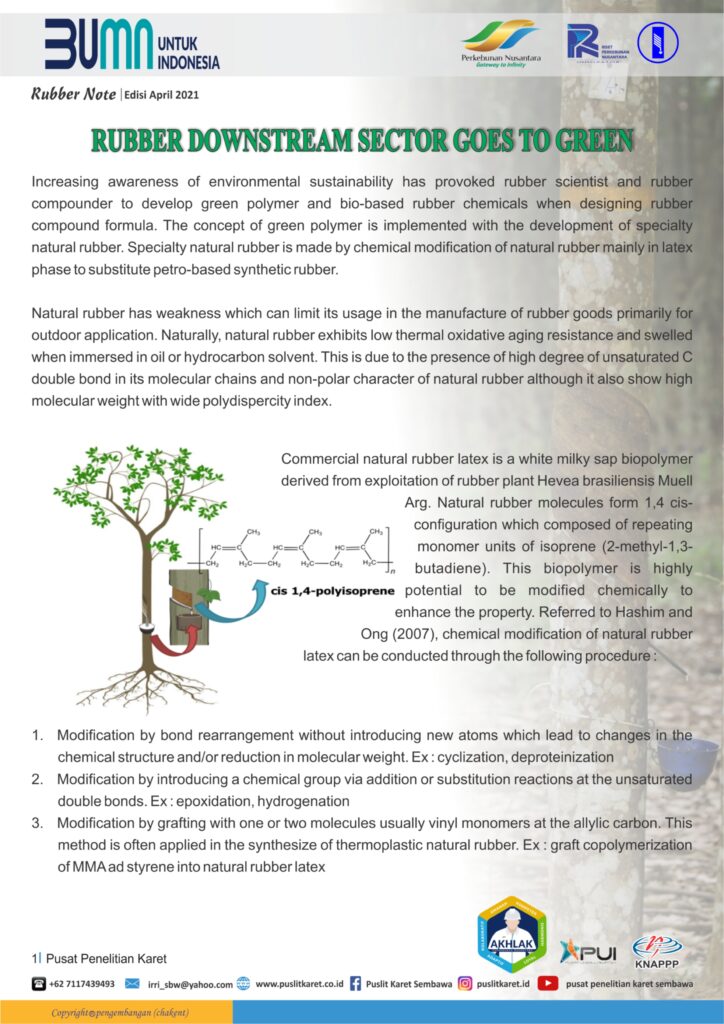
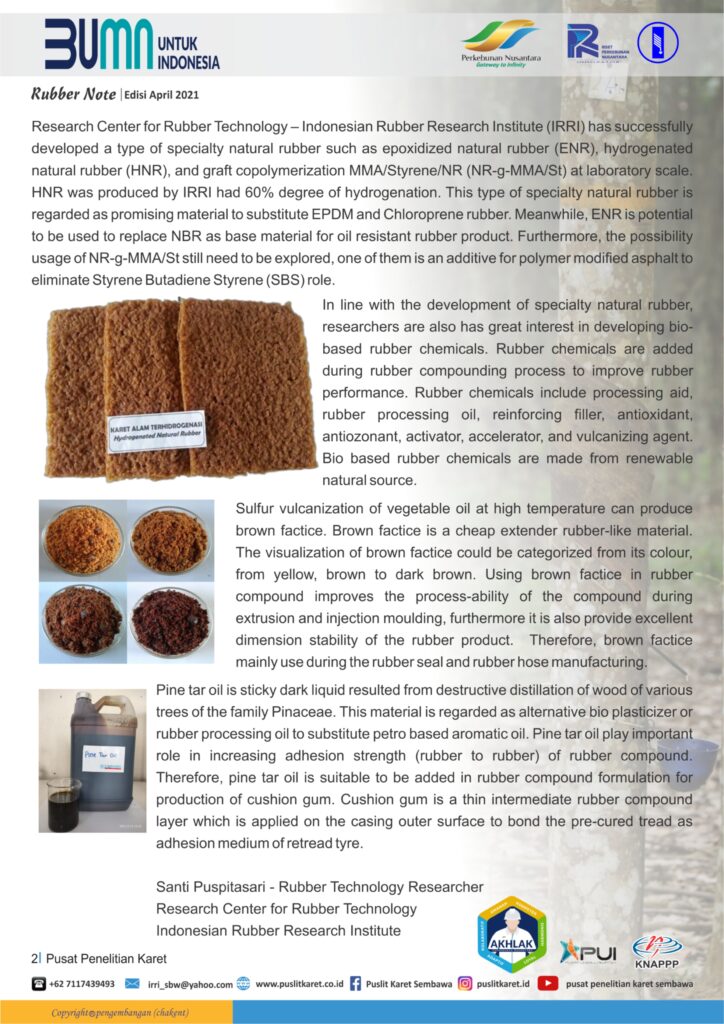